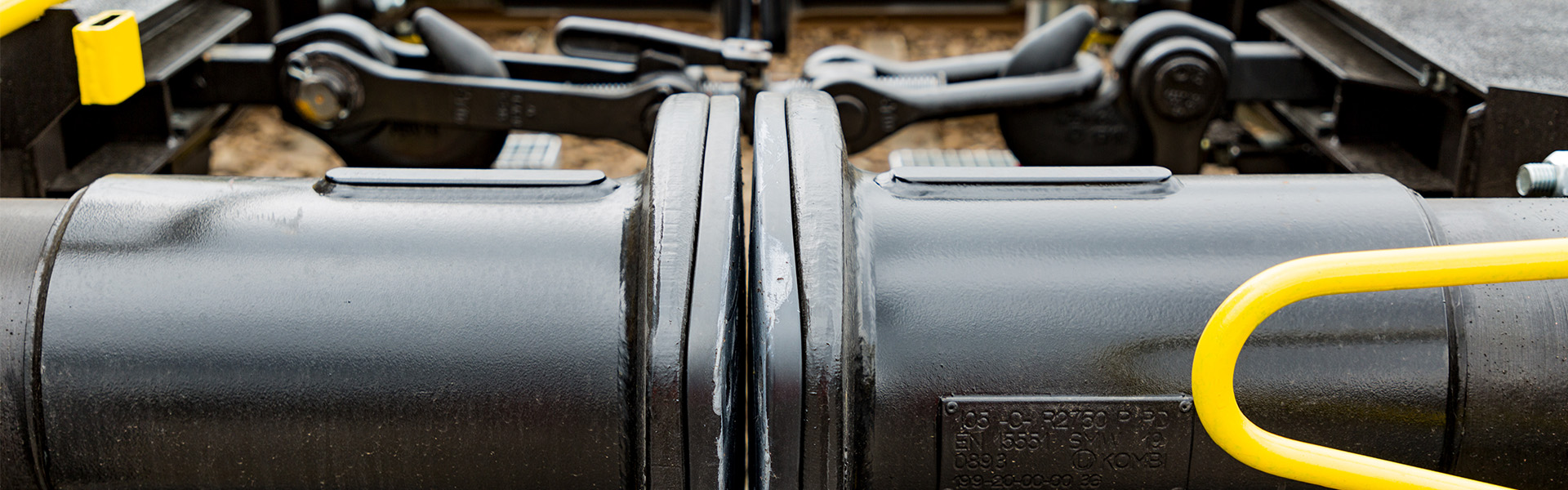
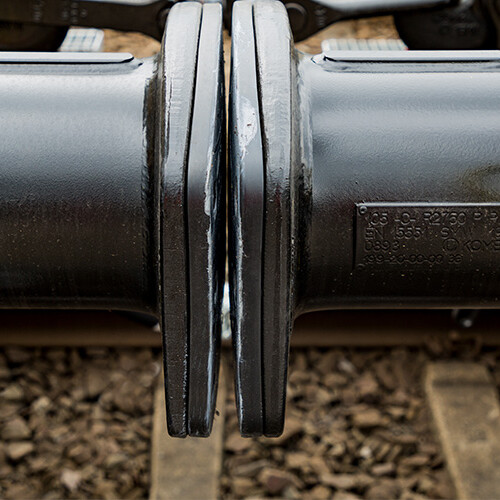
Philip Reinke and Christoph Petersen are the two colleagues from KombiRail Europe who have recently taken up their posts in Kombiverkehr's transport monitoring department at the company's headquarters in Frankfurt am Main. Together with the Kombiverkehr monitoring team led by Andreas Wilda, they form the joint monitoring and control unit for all trains that are already produced in the Kombiverkehr network by KombiRail Europe and will be added in the course of the current transformation by the end of the year.24/7, the two transport planners, together with other colleagues in Duisburg, cover both the so-called ‘long-distance dispatch’ and the local area with day shifts from Monday to Sunday and additional night shifts. This means that all trains on the route and the shunting services around the Duisburg DUSS terminal in Ruhrort harbour are under constant observation and permanent control. In the event of irregularities in operations, both intervene immediately and effectively. Locomotives are swapped, train routes optimised, train drivers sent to alternative pick-up points and, if necessary, transition times for incoming and outgoing trains at the terminals are shortened and extended. With success: since the start of the traction changeover to KombiRail Europe, a 100 per cent fulfilment rate has been achieved. Every train ordered by Kombiverkehr was dispatched by the KombiRail Europe team on the scheduled dispatch day and finally brought to the destination terminal. Even if a train was sometimes late, Kombiverkehr's customers benefited from a particularly high level of planning reliability for train departures, which minimised dispatching activities on the freight forwarding side for deliveries.
Synergy effects across desks
The main aim behind the merger is to achieve synergy effects, which has been a complete success: the causes and effects of events that affect the train schedule are exchanged across desks. Today, a Kombiverkehr employee knows at the same time where his colleagues Reinke and Petersen are pulling their strings and sometimes making the impossible possible. Previously, this was a kind of black box for Kombiverkehr. Each could only rely on the promised actions of the other. Today there is complete transparency. Simply being able to listen in and perceive the ongoing activities in the open-plan office brings calm and certainty to one's own work processes and customer information.
Being aware of what the other person is doing has now more than proved its worth. Not only for the Kombiverkehr team, but ultimately also for the hauliers' dispatchers, clear background information leads to even better documentation of train runs in the customer portal and to even more reliable arrival forecasts for trains and ETP times for the collection of loading units at the destination terminals.
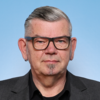
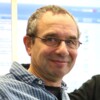
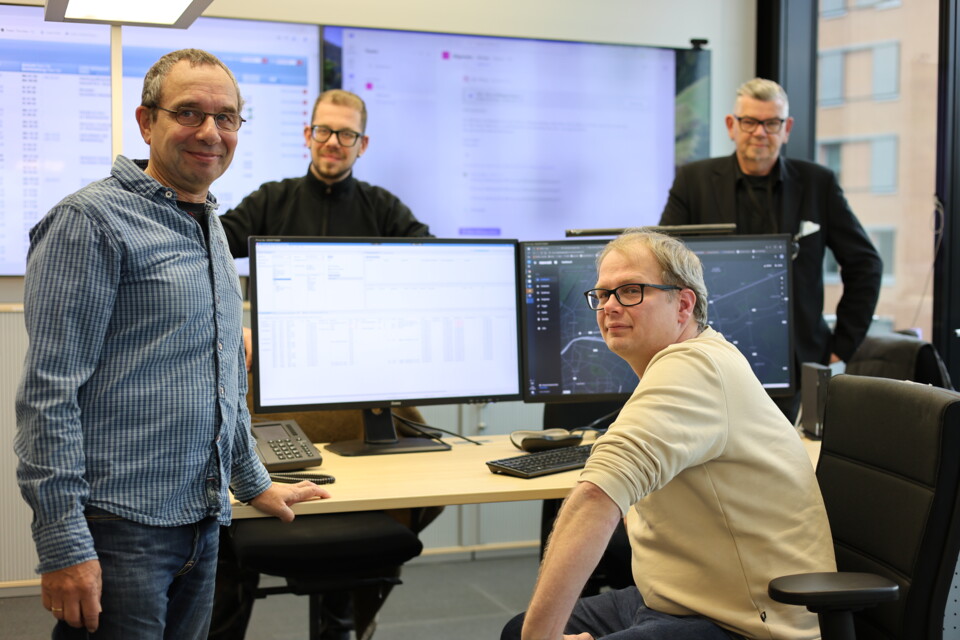
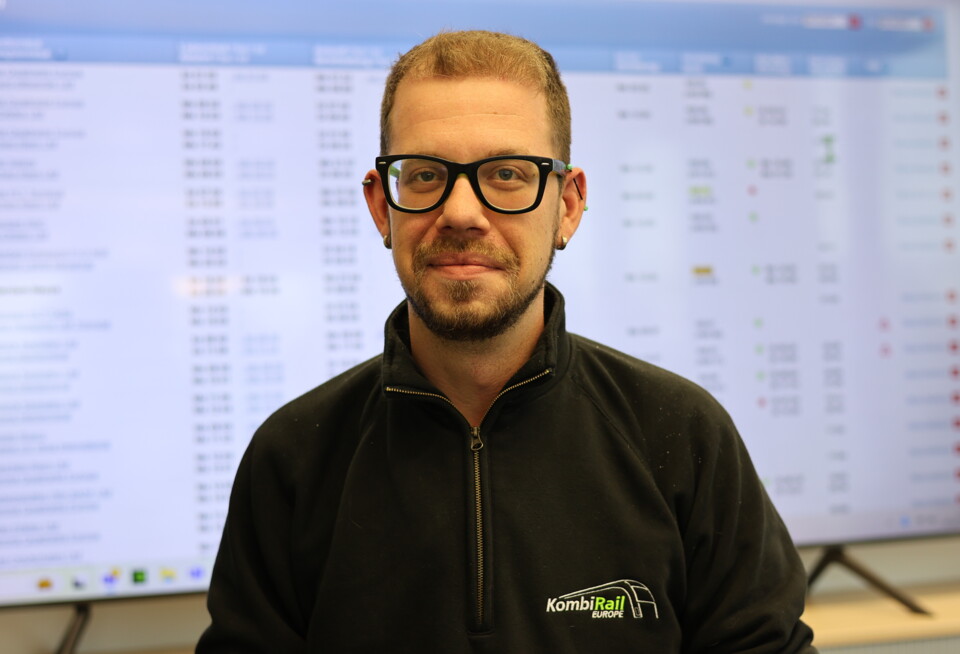
Age: 29
Apprenticeship as a transport service clerk
With KombiRail Europe since July 2024
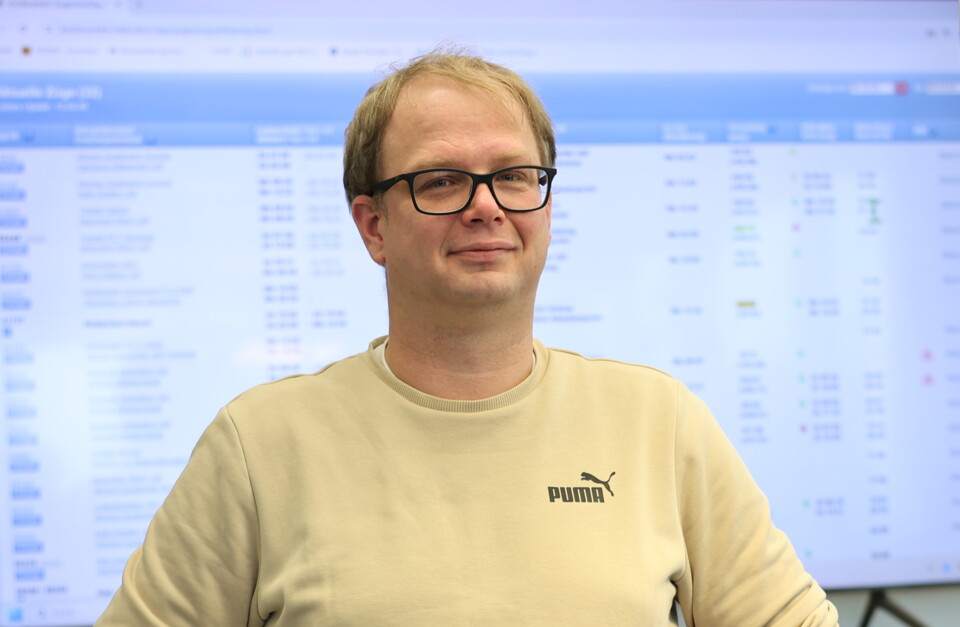
Age: 38
Studied Master of Arts in European History, then lateral entry at DB
With KombiRail Europe since July 2024
60949 Hamburg - Ludwigshafen: On 19 September, KombiRail Europe reports at 13:20 that the train is stationary in Bensheim due to a line closure near Weinheim.
A direct train from a third-party company - also bound for Ludwigshafen - is already at Bebra on 18 September. On 19 September at around 19:00, it is reported that the train is prevented from continuing its journey due to a line closure near Weinheim.
This means that both trains are on the line towards Ludwigshafen at almost the same time due to the same incident.
The following night, we receive information from the third-party company that there will be new information about the train's onward journey at around 8.00 am. At 9.06 a.m., however, we are told that Kombiverkehr will not receive the follow-up information until the afternoon.
KombiRail Europe announces in the afternoon of 19 September that train 60949 will be able to continue its journey in the evening. The train is diverted via an alternative route. Despite an additional delay due to a dangerous goods accident in the vicinity of the Ludwigshafen terminal, the train arrives at the Ludwigshafen intermodal terminal at 4.31 a.m. on 20 September.
The train of the third-party company arrives at the Ludwigshafen terminal two days later on 22 September at 12:41, after a new incident was reported near Bad Hersfeld on 20 September at 15:02.
KombiRail Europe managed to get five more trains to and from Ludwigshafen during the line closure, i.e. all the trains scheduled during this time.
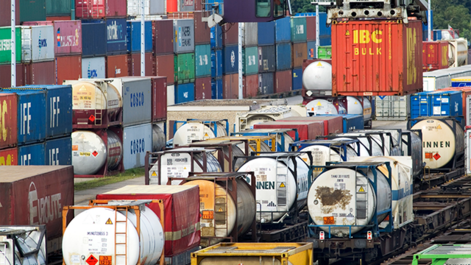
Connection Duisburg - Leipzig v.v.
KombiRail Europe is now responsible for and traction this connection.
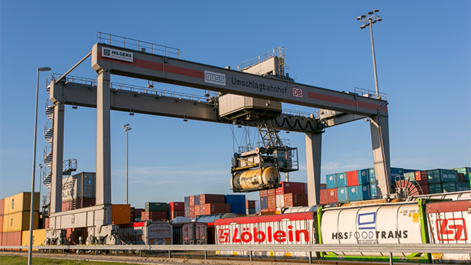
Connection München Riem - Leipzig v.v.
KombiRail Europe is now responsible for and traction this connection.
Of our connections to be converted are in operation.
The traction changeover requires a great deal of energy from a large number of players.One of these is the Dienstleistungsgesellschaft für Intermodale Verkehre (DIV). Our subsidiary specialises in fleet management and wagon maintenance with all the associated certifications. With currently 14 employees, the company managed by our authorised signatory Daniel Jähn is in operation at the two intermodal terminals Cologne-Eifeltor and Duisburg and ensures that the wheels of the wagon fleet are always in motion. As a neutral provider, DIV not only works for Kombiverkehr, but also for Mercitalia Intermodal, DB Cargo and many other well-known wagon keepers.
While the maintenance of freight wagons is already a challenging endeavour, wagon and fleet management is now a mammoth task: until now, Kombiverkehr has purchased the wagons (including wagon management) from DB Cargo together with the traction as a complete package. Now - as communicated - we are moving away from this concept to a considerable extent and hiring the wagons at our own risk. DIV will therefore manage a large fleet of wagons and ensure their efficient utilisation.
The task is challenging, but also unique
The challenge is to procure the specialised equipment on the market within the shortest possible time and to deploy it just in time on the relevant routes. To visualise the dimensions: We are talking about a pool of more than 2,500 wagons, which will be managed independently from the start of 2025. ‘The ramp-up is also a feat of strength for us,’ confirms DIV Managing Director Daniel Jähn. The task is challenging, but also unique for the entire team, he says. Everyone is pulling together, and together they have achieved all the previous milestones in the mega traction changeover project on time, summarises the 46-year-old, who not only manages the fortunes of DIV, but also the Infrastructure & Technology division at Kombiverkehr.
As far as the intermediate steps are concerned: ‘Since July, we have been transferring at least two routes to our own traction every month - in each case in conjunction with taking over responsibility for scheduling the wagons,’ reports Jähn. In September, the wagon fleet already totalled 299 units. This figure is set to rise to 409 by October. In the end, the aforementioned total will be more than 2,500 rail vehicles. This includes Kombiverkehr KG's own 361 wagons, for which DIV has been responsible for ECM for more than two years.
What is currently helping with the expansion of the large wagon fleet: ‘Availability is no longer the problem.’ This is due to the current weak economic environment. Another advantage is that there is already experience in hiring wagon fleets - in the past, for example, on the routes to and from Mortara in Lombardy or on the western harbour services for our subsidiary Optimodal. ‘So this is not entirely unfamiliar territory for us,’ explains Jähn.
Keeping the wheels turning and avoiding a standstill
DIV's main objective is to ensure that the wagons can be used and to avoid or minimise downtime as far as possible. In order to fulfil this requirement, DIV maintains its own mobile workshop teams at the Cologne-Eifeltor and Duisburg sites, which can carry out a wide range of maintenance and repairs in the open air. In addition, DIV co-operates with external maintenance technicians at all other terminal locations in order to quickly repair damaged wagons there as well. Worn brake pads are one of the most common types of damage.
Just as brake pads need to be changed regularly in cars, brake blocks on wagons also need to be replaced. Ideally, this can be planned. DIV therefore favours preventive maintenance. The aim behind this is to recognise wear or damage and rectify it as soon as it appears. If brake pads need to be replaced, the employees report this to the workshop at the next terminal, which in turn can prepare everything for the replacement and schedule the necessary resources.
All of this works without removing the wagon from service. ‘The main aim is always to repair the wagon in the wagon formation,’ explains the company boss. Both the intervention and the impact on operations are then minimised. If brake blocks are replaced too late, this can result in damage to the wheelset. This must then be replaced, for which the wagon must be discarded and made operational again on another track. In many places, DIV's own workshop team or its service providers also manage this task on a mobile basis. In most cases, however, a whole day has to be set aside for this and the wagon has to be scheduled for a complete round trip. But even this downtime is put into perspective: if the wagon has to go to the workshop, it can sometimes take two weeks or even longer.
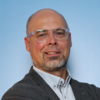
In order to effectively plan and control the use of trolleys, DIV employees need to know where the equipment is at all times. This is guaranteed with GPS tracking from the provider Nexxiot. The employees also use the ‘Echo’ IT solution from the Hamburg-based provider Aprixon for trolley management. In addition to resource and order management, Echo is also used to manage damaged wagons. It is also possible to plan repairs, create quotations for customers and much more. And in the future, other things are conceivable to make wagon management even more efficient with the help of digital tools. Managing Director Jähn is thinking, for example, of the possibility of predictive maintenance. The wagons are equipped with a large number of sensors for this purpose. These could report on their own when anomalies or defects are imminent. However, the use of such tools is still a long way off. And for the time being, DIV has to manage this one major project. From January, it may then have time for other things.
It is important to the DIV that the variance of the different wagon types is kept within limits. Depending on requirements, rail transport companies can draw on a large number of vehicle types on the market. The DIV experts estimate that 15 to 20 wagon types are in use in European intermodal transport. The company wants to keep the variety and the complexity associated with handling the wagons manageable. DIV primarily relies on the T3000 double-pocket wagon for trailers as well as four- and six-axle carrier wagons for different types of containers and swap bodies.
Little variety, standardised sets: The company also endeavours to keep the wagon sets on the individual routes as synchronised as possible. There may be typical routes for (tank) containers - for example to and from Ludwigshafen. There may also be tried-and-tested trailer routes - such as the Scandinavian services. Otherwise, however, DIV believes that many things can be standardised for rolling stock. The advantage is obvious: if the wagon sets are the same, they can be interchanged, which increases flexibility if one of them has to make a forced stop, for example.
Shortage of skilled labour everywhere? The DIV can only confirm this to a limited extent. It currently employs 14 members of staff; by the beginning of 2025, it will have 25 due to the additional tasks. And almost all of them have already been hired. Managing Director Jähn is pleasantly surprised that it has been easy to find trained fitters, vehicle technicians for maintenance and qualified business people for wagon management. The average age is under 40 and there is a great team spirit in the realisation of the new tasks.
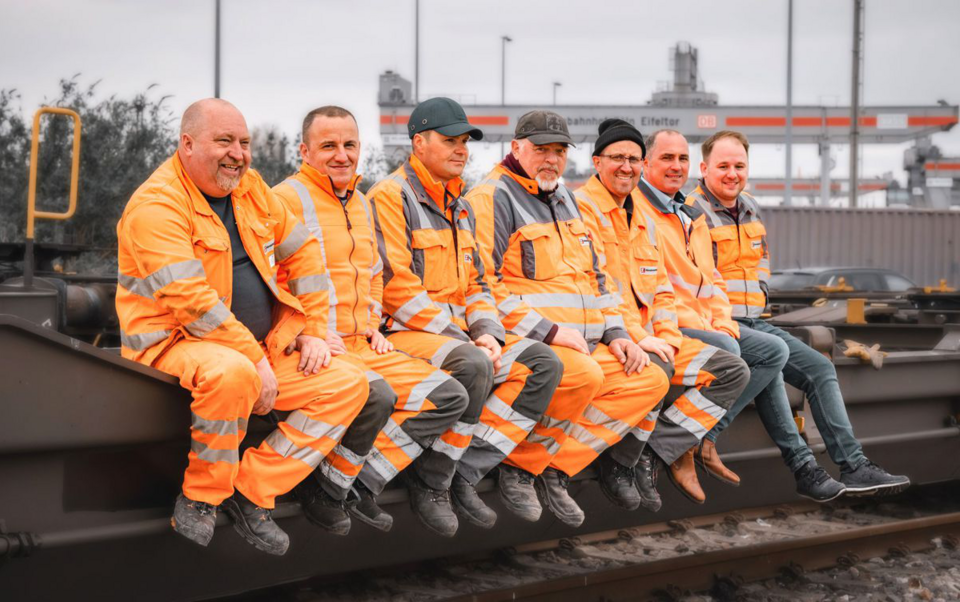